The Main Challenges of Flexible Automation
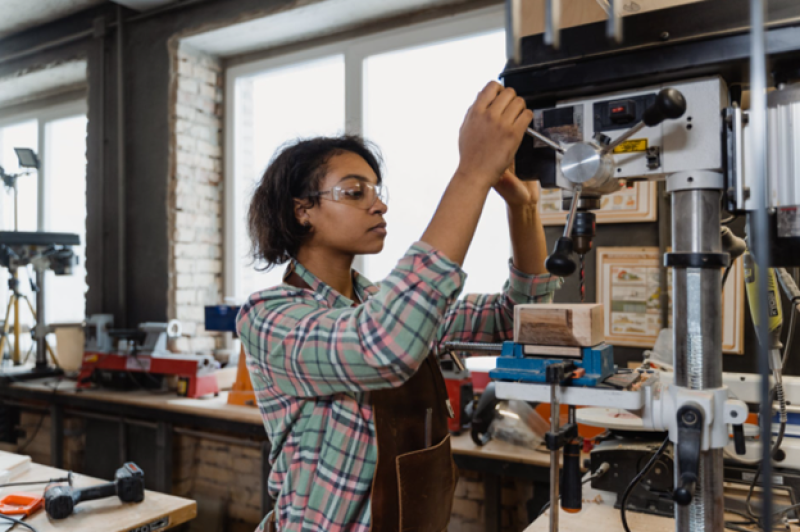
Flexible automation in manufacturing is becoming more prevalent, as companies are exploring the opportunities these solutions have to offer.
Flexible manufacturing systems are used to adapt to any changes within the production process. Since the second half of the 20th century, flexible manufacturing systems have supported organizations to produce goods more quickly and efficiently.
The main advantages of flexible automation systems include:
● Increased productivity.
● More efficient use of materials.
● Higher product quality.
● Better workplace safety.
● Decreased factory lead times.
On the other hand, automation does not come without its own challenges. Manufacturers have to make sure to assess and address these challenges, before adopting flexible automation systems in their production lines.
Here are some of the key challenges associated with automation:
1. High initial investment costs
Automated machinery can be expensive. This is usually one of the most conclusive factors that companies have to consider before committing to automating their production processes. A higher initial investment cost can be discouraging, especially for smaller companies, with less capital.
Conducting a comprehensive cost-benefit analysis before investment can support the decision, and provide valuable insights, including the timeline for implementation, and the return on investment.
2. The need for skilled labor
Operating flexible machinery requires a skilled workforce. The salary of these employees is generally higher.
Moreover, the maintenance and repairs on these systems have to be conducted by professionals.
This can either be done in-house, which can increase the cost associated with wages. Or companies can decide to hire subcontractors for this purpose. This reduces salary costs, but ad-hoc maintenance costs can be similarly high, or higher with the use of external service providers.
3. Complex implementation
Implementing flexible automation systems to production processes can be a complicated endeavor. It involves comprehensive planning, including the creation of detailed timelines, and schedules associated with the implementation.
Utilizing the expertise and support of external specialists can be a good way to help companies see the forest from the tree. Experts can help set up an all-encompassing, implementation plan, to support the adoption of the automation system.
4. Selecting the right technology
According to the findings of the IJITEE (International Journal of Innovative Technology and Exploring Engineering), the right automation technology is important because in many cases, using the wrong automation technology is worse, in terms of results, than no implementation of automation whatsoever.
5. Security concerns
Another issue that can arise from the current level of digitalization across the board, is the vulnerability of the underlying systems.
In our current times, manufacturing systems are usually built on open or standardized technologies to promote cost-effectiveness and efficiency. Because of this, most manufacturing systems are now exposed to online vulnerabilities the same way, as any other computer or software can be.
Security issues can be addressed with adequate measures, such as differentiating sensitive from generic information and using state-of-the-art software to detect suspicious online activities.
The bigger picture
Even though there are some challenges and issues manufacturers have to address before deciding to adapt flexible automation systems, these solutions can provide substantial benefits and returns.
These technologies allow companies to:
- Cut costs.
- Increase productivity and quality.
- Decrease human labor costs.
- Limit exposure to hazardous work environments and materials.
In the long run, flexible automation will be essential in creating safer, more productive, and sustainable manufacturing across industries, and enhance the quality of life of the employees.
As technology is progressing, innovative solutions in flexible automation are aiming to address some of the challenges associated with these systems.
The intelligent Plug’n’Produce screwdriver tool was designed to overcome the barriers of regular automation tools, and offer an easy-to-implement, inexpensive, and versatile solution to manufacturers.
Visit our website to learn more about this tool, or contact us for more information.
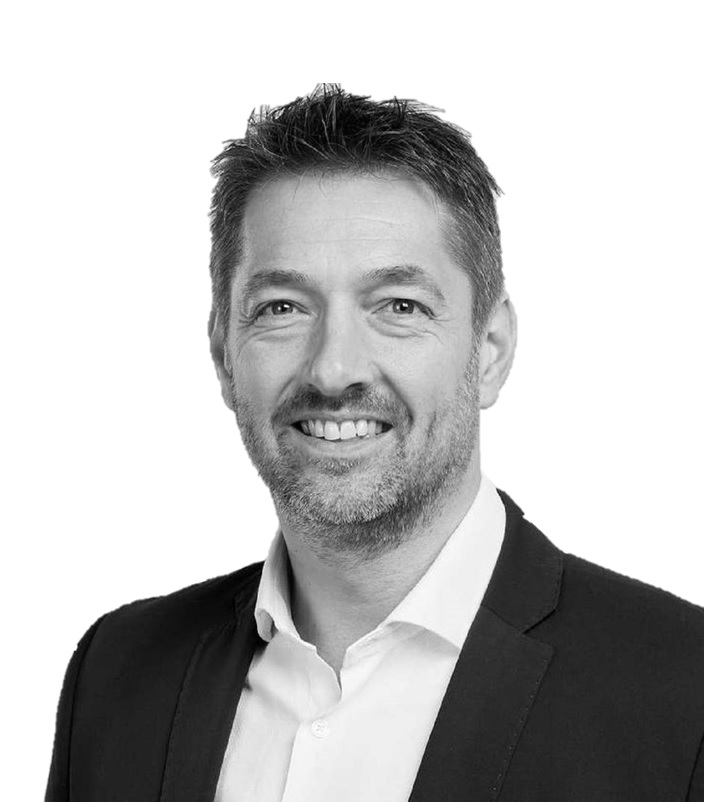
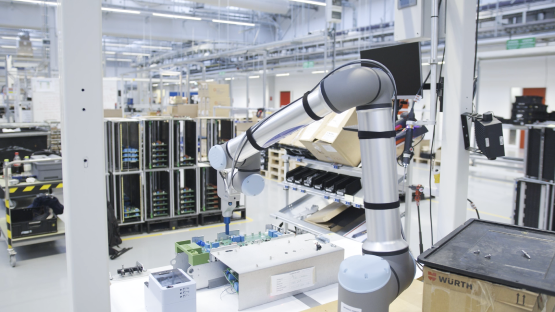