5 Things to Consider for the Most Optimal Screwdriving Processes
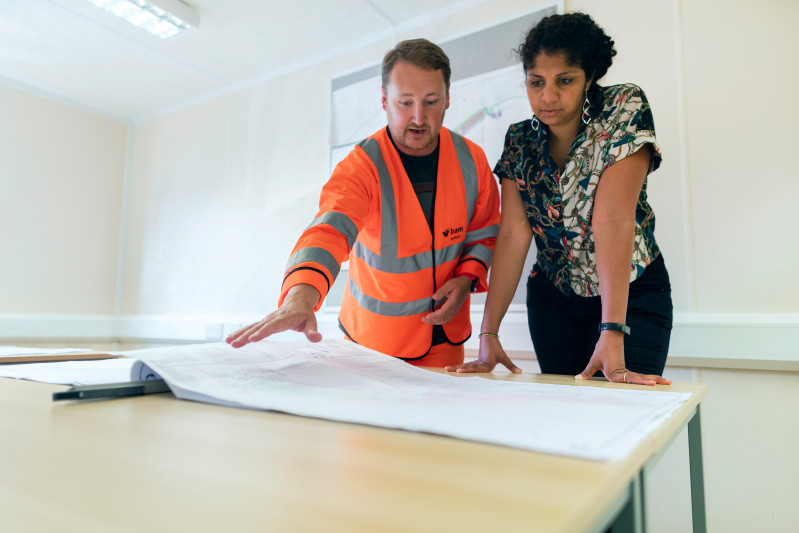
Often in an industrial assembly process, the complete screwdriver system, and not only the screwdriver needs to be adapted for the specific application it is used in. In each case, a variety of different attributes and external factors are considered, to ensure that the best possible solution has been selected for the task.
In the following list, we have collected the most significant aspects to consider in traditional industrial screwdriver applications and their downsides. The classifications provided here, however, are just a few of the many factors one should consider when selecting their tools.
1. Mobility
When considering traditional screwdriver options, one of the main considerations is whether the assembly is better served with a flexible or stationary (fixated) screwdriver system.
Manual screwdrivers are accessible and mobile assembly tools. These are recommended in case of shorter production cycles, relatively low volume, and a high variety of products. The downside of manual screwdrivers is that they require employees to operate them, which keeps them from accomplishing more creative and fulfilling tasks. Further, operating the same task for several hours every day causes joint pain in wrists and shoulders due to micro traumas from the pushback of the manual screwdrivers. Furthermore, manual screwdrivers are lacking in precise screws insertion.
Stationary screwdrivers on the other hand are better suited for assembly lines that require large volume outputs and long product cycles. These fixated assets are put to specific sections of the assembly line and are highly specialized for a given task. For example, in plastic-window and door engineering, stationary screwdriver systems are ideal for screwing in reinforcements. On the other side, stationary screwdrivers are highly inflexible, they can be only used for one specific task which still requires employees to operate them.
More advanced solutions are also available for the assembly lines today, in the form of automated screwdriver setups with collaborative robots (cobots).
Cobots are versatile and flexible, which makes them ideal to be programmed for different screwdriver tasks, with a wide variety of required parameters. Collaborative robots with automated screwdriver functions are state-of-the-art assembly solutions, which stand out among the top manual and stationery screwdriving systems. The Spin Robotics Screwdriver is easy to set-up within 10 minutes and doesn’t require employees supervising the cobot tool. Moreover, the screwdriver can be programmed for many different screwing tasks and is therefore extremely flexible.
2. Drive method
The most common types of screwdrivers in terms of drive methods are electrically and pneumatically powered ones.
Pneumatic screwdrivers are all corded and need an air supply to operate. This makes them considerably more bound in terms of workspace and accessibility.
However, these solutions can also be less costly, than some electric alternatives. Assembly lines, for instance, in the automotive industry can utilize these tools, when the sequence of assembly is specified, and compressed air supply is present.
Electric screwdrivers can be used in a broader range of activities, due to their relatively compact size, accuracy, and flexibility.
These can be used from furniture assembly to the aviation industry, with the right parameters in place.
3. Flexibility
The ability to change parameters (torque, angle, turn-direction, speed, or screw-depth) during assembly can be essential.
When a plant assembles different parts for a product, each part and step might have varied requirements. In an automotive assembly line, for instance, the optimal torque, angle, and other parameters of the assembly can be much different in the chassis and the suspension.
Moreover, the flexibility of a tool gives the assembly line the opportunity to switch its capacities to different products/goods on demand, in a relatively short time.
Setting up collaborative robots for automated screwdriving activities, for instance, can be performed easily, with short changeover times. Specific working parameters can also be adjusted on-demand. In automated screwdriving systems, flexibility is an inherent advantage.
4. Reliability
The reliability of the tool is among the most important factors manufacturers should assess before purchasing screwdriver systems. The requirements for process reliability always have to be determined by the specific task(s) it is intended to be used for.
In the case of some applications, operators only need simple feedback, such as “OK/NOT OK”, while in other cases they might need exact recordings, evaluations for each assembly step.
For instance, precision data like accurate torque measurements of the assembly are needed in the case of an aircraft engineering facility, while less or no recorded data might be sufficient for a furniture assembly plant.
When it comes to reliability and precision, automated screwdriving provides the most benefits.
Robotic screwdriver solutions provide a high level of reliability, that exceeds those of other forms in assembly, through their built-in protection functions, and precise torque control. Furthermore, the Spin Robotics Screwdriver delivers precise visualized data of the screwing process, providing indications on how to optimize the processes.
5. Cost implications
To get a full picture of the cost of each solution, companies should consider both the investment costs and the operating costs of the given screwdriver system.
Although, as the operating costs tend to be quite low in the case of both electrically and pneumatically powered screwdriver applications, the one-time investment cost of the item will be the real dealbreaker.
The price difference between the solutions can be significant, with highly specific, reliable manual screwdrivers and stationary systems being the most expensive investments. Although the Spin Robotics Screwdriver has a higher set-up cost than traditional solutions, it is extremely flexible, frees employees to do more important tasks, provides valuable data on the screwing process. Lastly, the Return-On-Investment on the Spin Robotics Screwdriver is shorter than other cobotic solutions.
With emerging competition in the field, advanced products are emerging in the market, and automated screwdriving solutions are becoming more available for manufacturers. As more companies realize the potential in automation, robotic screwdriving solutions are expected to become critical factors in shaping the future of industrial assembly.
The Spin Robotics Screwdriver will be available in 2021 Q1, contact us to receive a demo of our tool and help you realize your most optimal screwdriving process!
If you would like to learn more about screwdriver applications for industrial use, check out our Blog or visit our website.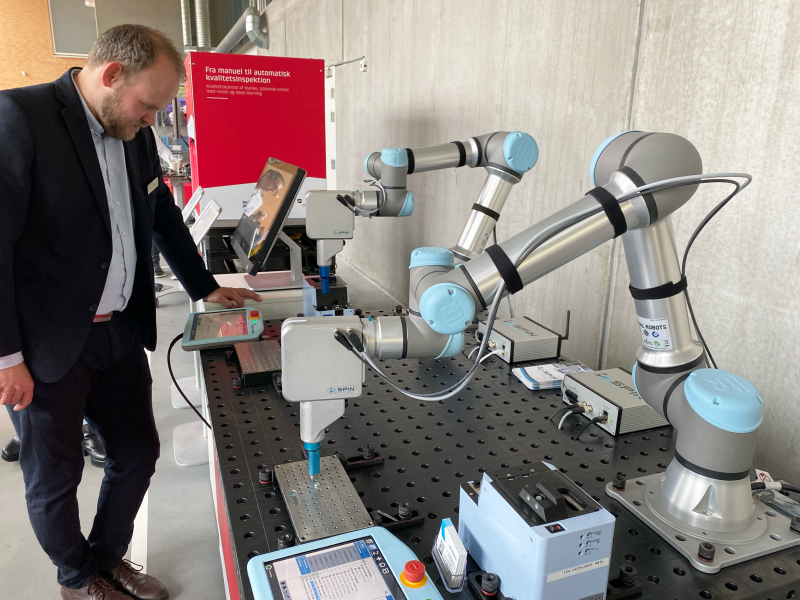
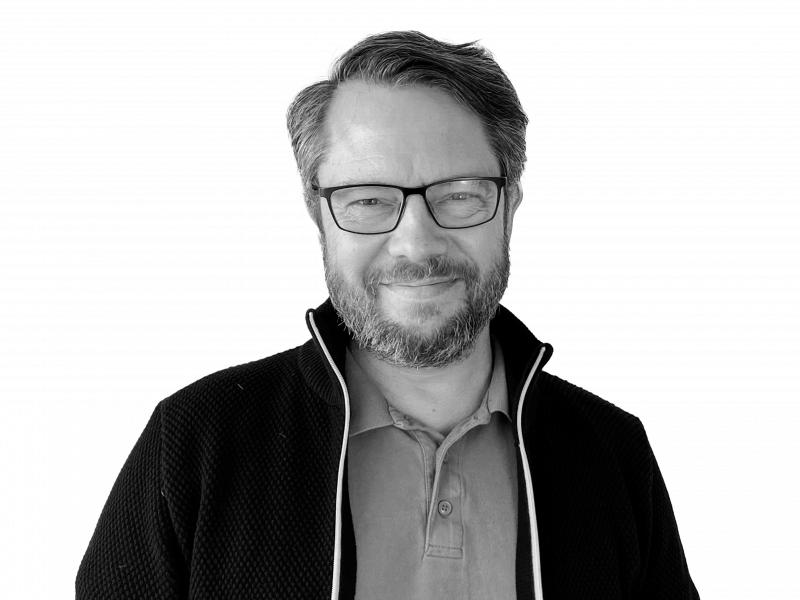
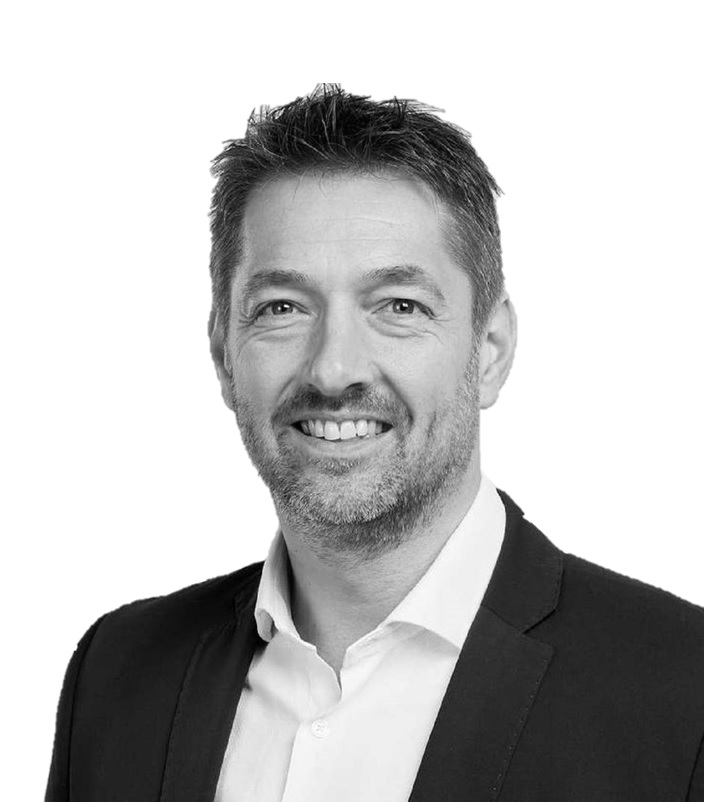
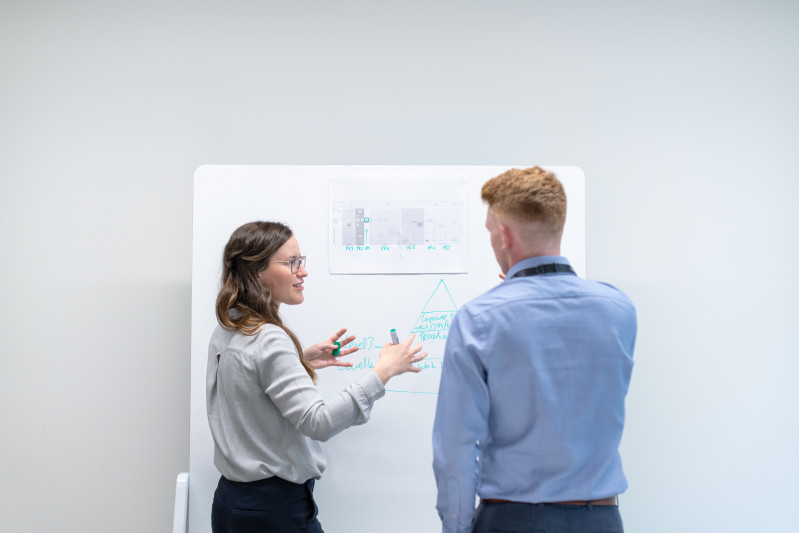
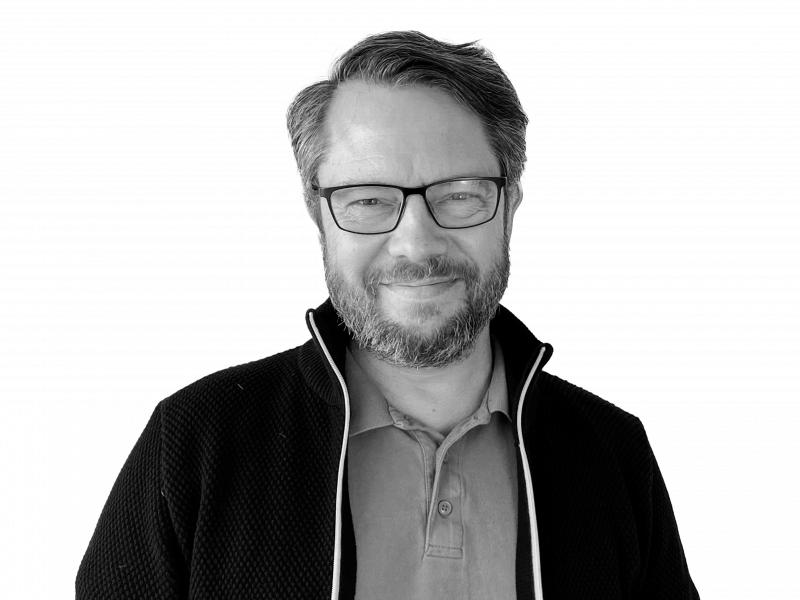
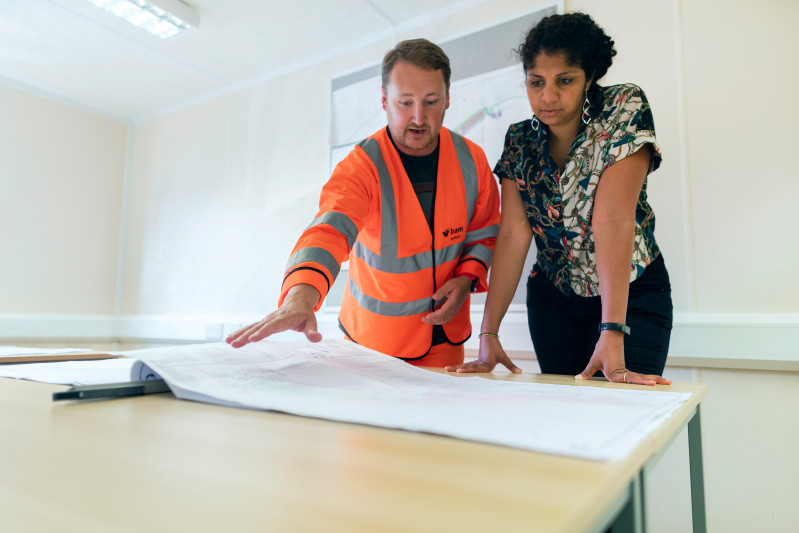
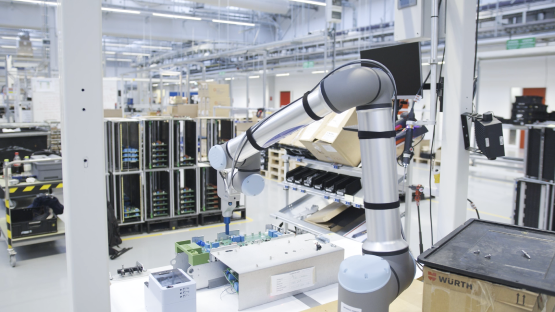