Cobots with Screwdrivers: The Optimal Combination?
As technology in automation is maturing, more companies get to exploit the benefits that intelligent solutions can offer. This results in higher productivity, better safety, and decreased costs for manufacturers.
Intelligent screwdriver solutions are overcoming the issues, that are mostly associated with the traditional assembly practices.
The Shortcomings of Manual Screwdriving and Traditional Automation
Manual screwdrivers used to be the go-to solutions in assembly through many industrial applications. Their importance, however, is becoming less and less significant as automation creeps into almost all the areas of manufacturing.
Using only manual screwdrivers can result in variable output quality, unpredictable cycle times, absenteeism, and less stable production in general.
Traditional automated screwdriver solutions can offer much better productivity, can reduce cycle-times, increase the quality, and move employees from the assembly lines to more value-producing activities.
However, highly specific, automated screwdriver systems are usually quite expensive, require complex programming for initial setup, changeovers take a long time, and error-proofing can be problematic as well.
Due to the higher costs, and the specificity of these assets, traditional automation in assembly is generally more beneficial for large production volumes and is more accessible to big enterprises.
The Power of Cobot-Enhanced Screwdriving Solutions
Collaborative Robots (Cobots) are designed to work safely alongside human employees while enhancing productivity, and quality by removing workers from strenuous, hazardous, and monotonous physical tasks, such as the assembly of various workpieces.
Today, robots and cobots are less expensive than in the past, due to the maturation of these technologies, and are more readily accessible to smaller manufacturers as well.
Robotic screwdriver systems that are designed to be used by cobots are ideal for flexible production, assembly applications that require high torque, multiple fasteners, and quick changeovers.
Intelligent screwdriver solutions, that are compatible with cobots can have additional benefits for companies:
- Simple setup and configuration process
Easy setup and configuration is a major benefit of these systems, which allows companies to save time, and expenses from complex setup processes.
- Return on investment
Investing in an intelligent screwdriver solution that can be used by cobots, allows companies to lower their prices and beat competitors in the market, in a short time as 10-12 months.
- Safe around employees
After a brief risk-assessment, these tools can be used safely, and efficiently alongside human employees.
- Shorter assembly and changeover times
Time is one of the most critical aspects of manufacturing and assembly. The time needed for assembly and changeovers can be reduced by more than 40-60%, with the use of intelligent screwdriver solutions and cobots.
- Data-supported quality monitoring
With the integration of advanced data tracking and analytics tools, quality assurance is much easier than it used to be in the past.
The online quality assessment allows manufacturers to look into the data about the torque values of each individual screw, or detect insertion failures before the specific item leaves the assembly line. This greatly reduces the chance of quality issues, and downtimes.
To learn more about our Intelligent Plug’n’Produce Screwdriving Tool, visit our website, or contact us directly for more information.
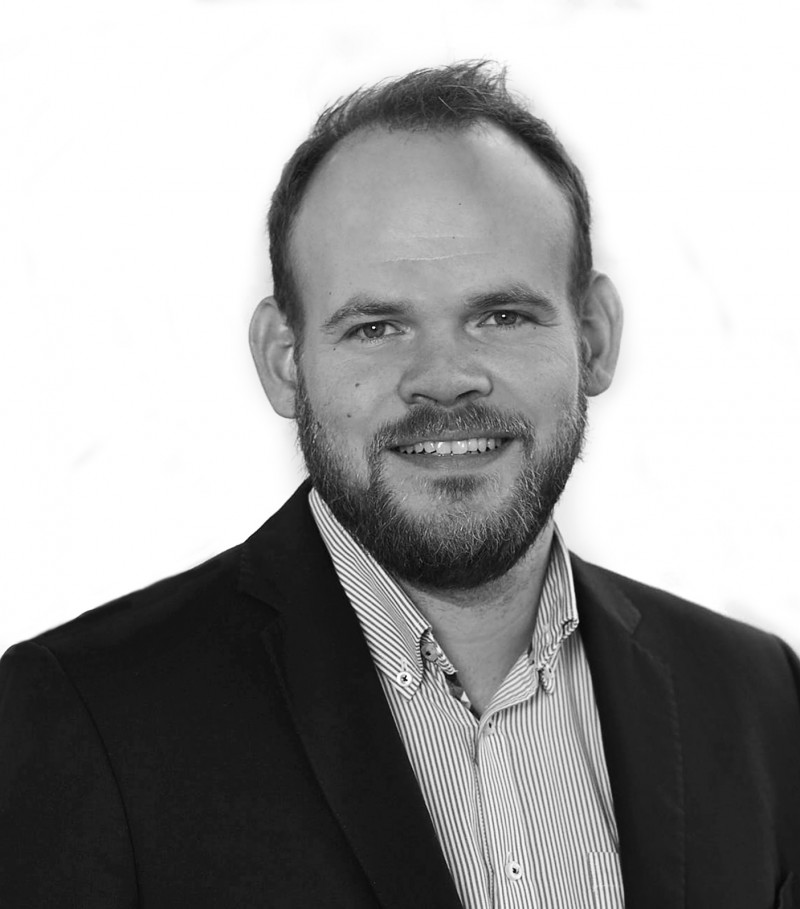
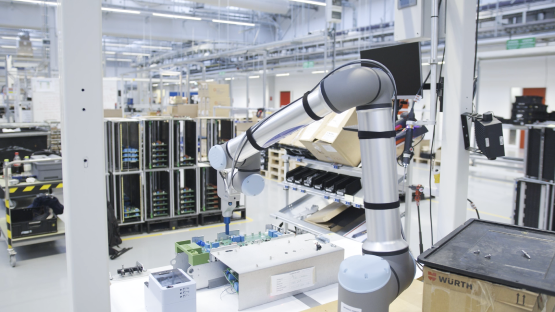